Could recycling end-of-life concrete in electric arc furnaces hold the key to zero-emission cement? European Energy Innovation speaks with Dr Cyrille Dunant from the University of Cambridge, where researchers may have cracked one of industry’s hardest problems.
Cement is the cornerstone of our built environment. Worldwide, we consume around half a tonne of it per person per year – an astonishing figure that reflects its unique strengths, unparalleled versatility, and consequent ubiquity in virtually all construction projects.
Its production, however, remains a significant environmental challenge, accounting for some 7.5% of all anthropogenic CO2 emissions. And while efforts have been made to mitigate this impact, through both tweaks to the manufacturing process and by carbon capture, it remains impossible to replace and incredibly difficult to decarbonise.
But researchers at the University of Cambridge might have found a solution. By recycling end-of-life concrete, reclaiming the cement and adding it to an electric arc furnace at the same time as recycling steel, his team found that the result was recycled but usable portland cement – a discovery that changes the way we think about concrete, the world's most-used material.
"We've found that cement is in fact a recyclable material," says Dr Cyrille Dunant from the University of Cambridge's Department of Engineering.
"It can be recycled at the same time, and in the same facility, as recycling steel. And because this process uses existing industrial equipment and infrastructure, it can be scaled rapidly as an alternative solution to the old way of making cement."
Put simply, Cyrille and his team have found that 'second-hand' cement reclaimed from old buildings is a good substitute for the lime used in the recycling of steel, and that the by-product can be used to make more cement.
Normally, the lime is used as flux and effectively floats to the top of the molten steel, to be scooped off as slag and discarded. But if you put cement paste in there instead of the lime, the resultant slag contains clinker – the precursor to cement.
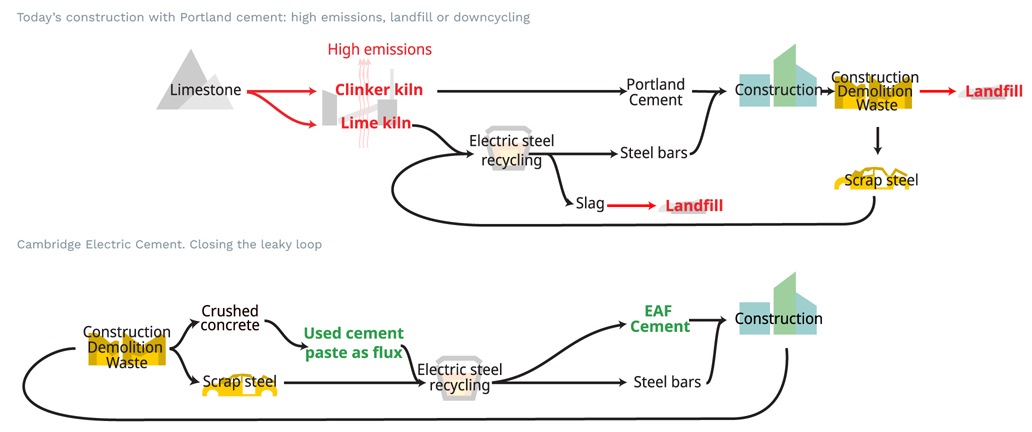
This has significant implications. Firstly, the idea that concrete is recyclable is pretty revolutionary, and comes at a time when end-of-life concrete structures are becoming abundant. But more importantly, the recycling of steel can take place in an electric arc furnace which – provided the furnace runs on renewable energy – implies that zero-emission recycled cement is a viable possibility.
"We have opened the route to electrifying cement recycling", says Cyrille. "That's quite important, because normally there's no way of electrifying a high-temperature process for non-conductive material. With a conductor, you can zap it and it'll heat up, but cement is a nonconductor. The trick is to zap the steel, and the steel then provides the heat to the cement."
It sounds relatively simple. So why hasn't it been done before? Cyrille says that the primary reason is economic, rather than technical.
"Concrete is very cheap," he says. "Recycling materials that are very cheap is a bit strange – unless you can make it even cheaper. The other reason is the energy required for the high temperatures. If you burn fossil fuels you make some savings, but not great savings. And if you don't make savings you're not going to make it economically viable."
Economic viability and scalability are next on the project’s agenda. The researchers have worked with partners in industry, including Celsa, Tarmac, Atkins and Balfour Beatty, and have founded a spinoff company, Cambridge Electric Cement.
"We have a whole range of partners," explains Cyrille. "It's important to have a complete supply chain of partners to be able to understand how everything would need to be reorganised so we could make the recycling viable. It really is a team effort. We have the idea, but it'll only make an impact if we can make it work really well."
"And that involves a lot of people, who all do their job very well and in very optimised ways. And crucially they are not used to working together. The steel and cement industry – traditionally they're like oil and water, they don't work very well with each other. But here we're proposing a way for steel and cement producers to form a team, because they coproduce and co-recycle. So there cultural aspects to this as well."
It's interesting to note that the world's two dominant building materials have such different life cycles. Steel is the world’s most recycled material, but recycling cement is virtually unheard of. Cyrille thinks that there's a significant untapped market for recycled, low emission concrete, as well as other efficiencies to be made in cement based construction.
"It's under-appreciated, but there's a huge pool of consumers," he says. "If I'm developing homes, or building infrastructure, I am often ready and have a budget for lower impact products and practices. And frequently the buyer is not so budget-constrained, it's that the products aren't there. Adding options is helpful at this stage.”
Together, the EU and its Member states turned a historic threat into an equally historic opportunity. These foundations are our legacy and the basis for our work ahead.
"Concrete mixes are quite inefficient," adds Cyrille. "We could be making concrete just as strong as today with slightly better grading of aggregates."
"Typically today we use 350 kilos of cement per metre cubed of concrete, that's your typical ratio. It would require a change, but you could well do with 250kg and you could produce concrete just as strong. Design is another thing. Big savings are possible."
There are obvious hurdles to overcome, both technically and practically. But the breakthrough has been described as "miraculous", while Julian Allwood, Professor of Engineering and the Environment at the University of Cambridge, says it could be "one of the biggest material breakthroughs to come out of Cambridge in the past few decades". We ask Cyrille how long it will be before a building can be built using recycled cement.
"We've made quite a few samples," says Cyrille, holding up a battered block about the size of an apple. "We've produced the stuff and tested it. But the next big step is understanding the quality and how to reliably produce it."
"We're already doing trials at scale with our partners, trying it in a full-scale electric arc furnace that recycles something like a million tonnes of steel per year. We're fairly close, so this is not something for 20 years – perhaps more like four or five years. We're optimistic. But you know, famous last words."
